![The_Weaving_of_Thoughts_copy[1]](https://edswoodturning.com/wp-content/uploads/2010/12/The_Weaving_of_Thoughts_copy1-150x150.jpg)
The Weaving of Thoughts by Doug Fisher
Recently our guild hosted Doug Fisher for a one day demo and one day workshop. For those of you who are not aware of Doug’s distinctive style, I have included a couple of pictures of his signature pieces. Typically he turns wall plaques with multi-centered “frames” around a center area carved in Pacific Northwest native themes. I was fortunate to attend not only the day long demonstration but the one day workshop as well. Spots in the workshop were hotly contested and I was one of the lucky ones to get my money in before several others that had to sit this one out.
Following is the article that I will be submitting to the guild’s January newsletter. Remember, you saw it here first. 🙂
![Predicting_the_Past_640[1]](https://edswoodturning.com/wp-content/uploads/2010/12/Predicting_the_Past_6401-150x150.jpg)
- Predicting the Past by Doug Fisher
Doug Fisher Demo and Class
On November 13 and 14 Doug Fisher demonstrated his well known techniques of multi-center turning and bas relief carving. Doug has not had a long career as a demonstrator. As a matter of fact his demonstration for us was only his third, the first being for the AAW symposium in Hartford last year and second for a Victoria, BC guild. That being said, I would say that Doug is a natural because his well organized and polished presentation seemed as though he had been delivering his show for quite some time. Doug started with a brief slide presentation tracing his advancement through his artistic career to the present day, then describing what inspired his distinctive turning style as well as his use of native Pacific Northwest themes. After that he demonstrated both his turning and carving techniques to round out a very full day.
Doug’s signature pieces are a combination of multi-center turning to produce a frame or armature for his carving in the center. I think the term “armature” is applicable because the works that Doug produces are as much sculpture as they are turnings. Although his multi-center style seems quite complex it was a simple combination of two centers. Doug turned the back of his demo piece first, producing a rather large radius resembling the outside of a bowl with no detailing or foot. Although there was no center detail required, Doug often incorporates a center “medallion” to provide a bit of interest. The purpose of this radius was to act as a rocker allowing him to orient the centers anywhere he wants in a vacuum chuck. Having used a faceplate to turn the back, the piece was remounted on center in the vacuum chuck to work on the face. At this point, only the outside rim and the first series of “steps” were turned as well as removing the center waste material. When removing waste from the center, he was careful to only remove material to the diameter and depth where the holes were from the screws used for mounting on the faceplate. This would eliminate the possibility of any screw holes showing up inadvertently when it was too late to do anything about them, yet not take any more material than necessary.
The piece was remounted by rolling the piece in the vacuum chuck to a second center about 2 inches away from the first or natural center. He explained that it is important to place the off-center pattern in line with the grain direction so that it doesn’t result in a confusing pattern. When he showed us the alternatives it was clear that this was an important step. The distance of this center from the true center is somewhat arbitrary; however discretion must be used to allow enough material in the center for a reasonable carving surface; in other words, move it over a bit but not too much. Turning this area reminded me of the off center turning demonstrated by Mark Sfirri. The procedure involved turning a fair bit of air and using “ghost” forms as guidelines. A series of steps were turned that partially cut into the first steps on an angle, being careful not to cut into the center area needed for carving or go past the outside diameter (like we would ever do that :)).
Remounting to the natural center for a second time allowed him to turn a convex curved surface that would be the final carving area, now surrounded by the two sets of eccentric steps. Although this area is on the natural center, it is offset from the last center so the same process of turning air and using ghost forms for reference was required. The main form was complete at this point, ready to be carved.
Doug’s process for laying out the center detail was quite simple, although developing that process took quite some time. Doug uses a draw program in his computer to produce a print of his final detail. This sounds as if it is a “cut and paste” operation but he hand draws the detail using the program. This allows him to adjust the size of his drawings as required and also keep a record of his work. Doug had shown us pen and ink drawings that he had done prior to his turning career so it was clear that the computer was not his source of talent. The print is made from that drawing then cut out to fit the area being carved. Spray glue was applied to the back of the drawing which was then applied to the area to be carved. The small amount of distortion between flat paper and the slightly curved surface was insignificant. The carving involved removing any wood that would be negative space using the drawing as a guide. Depending on the complexity of the detail, negative space was marked out to differentiate it from the areas to be left in relief. Transferring the drawing to the wood was easy enough; carefully burning through the paper with a fine burning tool left a burned tracing of the drawing on the wood that was very easy to follow. The paper drawing and glue was then removed with solvent.
The final detail was carved in three stages. The first stage was the rough removal of material using various rotary carving bits, being careful not to remove any detail lines. The second stage was completed using various finer bits to get closer to the lines, still being careful not to remove them. The third stage involved using a burning tool to refine the detail right to the lines, making all lines and corners clean and crisp. All negative space surfaces were textured as desired using combinations of rotary carving and pyrography.
Once the carving is complete, a base coat of black ink is applied to the whole piece. Once that is dry, a process of sanding back the relief areas reveals the details of the piece in both the carved center area and the stepped frame areas. By varying the amount of sanding in different areas, visual depth and highlights are added. At this point coloured dyes are applied to the sanded areas.
Doug uses alcohol based dyes and at one time used several colours but now only buys the primary colours, red, blue and yellow. He is able to mix any colour from these base colours. The dyes were applied carefully with various brushes depending on how small the areas were that were to be coloured. His top coat is always spray lacquer from cans – usually semi gloss.
The workshop was held the next day at Island Woodcraft, attended by Bruce Campbell, Joel Elder, Jay Mapson, Bev Pears, Des Wilson and myself.
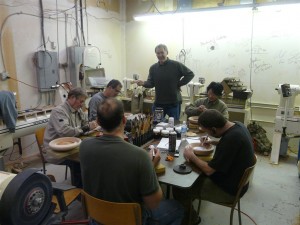
- The class at “work”. Bruce is getting a scolding.
Once the blanks were cut, we started by mounting the piece to turn the back. Doug pretty much does this in his sleep but he had made some profile jigs for us to use as guides for a suitable radius for the back. A key element of Doug’s process is the vacuum chuck and of course at most, there might be one vacuum chuck in a shop. Doug developed a method of using screws through a short section of 4” pipe between a faceplate and the workpiece to mount and remount the piece for turning the face. This was a pretty good simulation of a vacuum chuck. The screw holes left in the back of the piece were easily removed by jam chucking the piece and turning a concave detail on the back. This served nicely to provide flat wall mounting.
Once mounted to turn the front, turning the outside rim and steps on the first center certainly was easy enough, however when remounted on the second center I was quickly reminded of the difficulties experienced in Mark Sfirri’s workshop, looking for the elusive “ghosts” produced by the spinning wood when offset from center. Working on centers in Sfirri’s class was significantly different because this work was mounted on the face. Difficult at first, it soon became easy enough to identify the various points where wood had been removed and where it was yet to be removed. I found that looking straight at the face of the piece rather than down toward the ways as we did when turning between centers was the charm.
Turning ate up the whole morning so a natural break allowed us the opportunity to head over to the little Vietnamese restaurant for lunch. This is becoming a favourite part of the day in the workshops. Once back from lunch we were able to start carving. We all had a drawing to apply to the work or at least some idea of what we wanted to do. As well as our own collection of tools, Doug supplied us with all manner of instruments of destruction. We were all able to rough out and refine detail on our pieces using tools supplied by Doug and trading our own tools back and forth.
Applying the ink that Doug supplied is a little different than the black dye that I normally use. It’s thick! And black! I made the mistake of applying it like the dye I use in my shop (I can use a lot of it) and then proceeded to sand my fingers to a nub just to get some wood clear enough to accept some colour. I actually got one highlight area that I had hoped for, but fatigue set in and that was the end of that. Surprisingly, it was actually identifiable as a Harley Davidson engine (big surprise, huh?) but only to an enthusiast. At this stage I was slapping on some colour and lacquer just to get finished. I’m not used to working to a “close counts” standard, but in this case it served the purpose. We were reminded that “this is your first piece, not a masterpiece” so I felt better about basically hacking a design into the wood just to get a finished piece. My objective was to go through all the processes and for once, being happy with something that was “good enough”. In this case “good enough” was still pretty shabby in my opinion, but I felt practicing all the steps was more important than not completing a finely detailed piece. In the end it wasn’t all that bad and was at least identifiable when I proudly showed the piece off at home. I was able to write about the process here more than a month later because working through the process locked it in my brain.
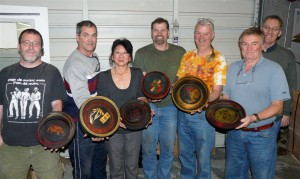
Graduating class and teacher.
The most important thing about the day was that we all had a lot of fun and learned some skills that we didn’t have before. The most prominent aspect of Doug’s work is the native theme that he uses. That isn’t my style and had I focused on that rather than wanting to learn the different processes that he uses, I wouldn’t have taken the class. I made that mistake when I missed Tania Rada, but not this time.
As always, I encourage your comments and questions, so please refer to the tag line at the bottom of the article to post a comment.