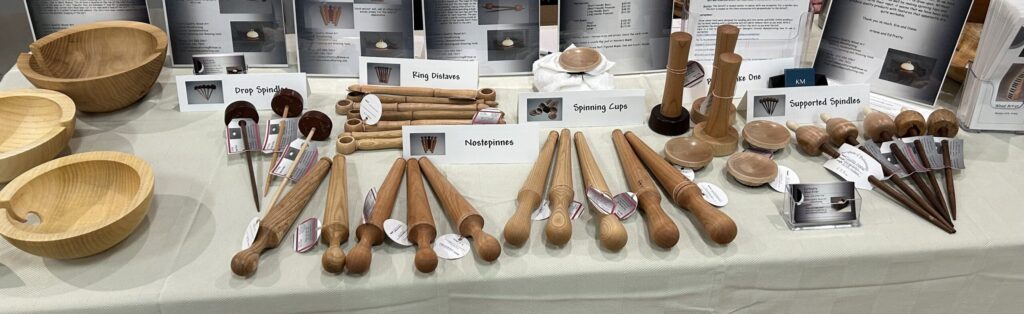
Recently I was asked by a fiber artist to make drop spindles. I had never heard of them before, so a little research was in order. My first impression – from photos – was that it was no more than an upside-down top. I couldn’t have been more wrong! I suspected it had to be more sophisticated and I was right. Fortunately, I was directed to two very knowledgeable fiber artists, Kim and Diana. Not only were they very experienced, more importantly they were very keen to pass on their wisdom.
Wood Choice is Important
I felt I should master one implement before moving on to the next. I started with drop spindles then moved on to supported spindles. I am quite familiar with wood densities and physics so understanding the dynamics of spindles came relatively quickly. Adding the various practical features that Kim and Diana suggested made the move through the prototypes an interesting journey. Typically, I use a dense, straight grain wood for the shafts; eastern maple is ideal for the smaller drop spindle shafts while that and black walnut works well for the slightly larger supported spindles. Denser woods that are more suitable for the whorls are typically the more “exotic” varieties, of which Mahoganies, Rosewoods and my very favourite – African Blackwood – are excellent choices. Some of these woods do not require a finish because of their high oil content, creating a lovely soft sheen. We have a few locally grown species like Acacia and even Black Walnut that also work well. Lighter woods like figured Big Leaf Maple work but the whorls are larger, which affects the spin dynamics. That being said, the appearance of fiddle back, quilt or burl maple when coloured is spectacular!
While on the subject of exotic woods in particular, I make use of reclaimed wood as much as possible and when milled specifically, I ensure that it is ethically sourced. I have a block of Lignum Vitae which is now illegal to cut but was purchased by a friend many years ago. It will be used for very limited editions of both suspended and drop spindles.
Making: What I do
To me as a woodturner, feel and function is important in a tool and as a wood artist, aesthetics is equally important. I like colours that either compliment or contrast, surface textures that feel good in the hand and woods that will make it possible to do the job intended. This is my opportunity to combine woods that I like to turn and like to colour, to make tools that are pleasing to the eye and that are satisfying to work with.
Other tools like ring distaves and nøstepinnes are really fun to turn and I make them from hardwoods that both look good and make a lasting tool that feels good in the hand. Eastern Maple, Big Leaf Maple, various Oaks, Black Walnut and Ash are all durable, attractive woods. Wooden tools develop a patina over time from constant use and contact with fabrics, and that only makes their appearance better. Eastern Maple is ideal for niddy noddys and it holds the hardware I use for switching the center shaft very well.
Dizzes are new on the list but the harder woods that are suitable for whorls are also suitable for dizzes. I suspect the fiber being drawn through the hole could cause wear over time, so softer woods would not last. Kim is working with me on a design that will be very functional.
Some tools are still on the horizon, dealigans for example. I can see that a variety of woods would be suitable for them. For me, they look like they will be fun to turn so I’m looking forward to that. I understand that spinning flax is becoming more in vogue which will require an addition to some, if not most, spinning wheels. I have prototypes in the works and they will be made from Eastern Maple. It’s hard, strong, wood that will get the job done and the appearance will closely match the small variety of woods used in most wheels.
Custom Work and Repair
Although I am developing a “line” of tools for fiber artists, I am prepared to work with anyone who needs something custom made. For instance, if a particular style of working requires a modification, or in cases where physical requirements (like small hands) require modifications to a design.
I have also learned very quickly that spinning wheels break down in various ways. Our very first outing at a spinning retreat found me making repairs on the spot and later that week, so it appears that I am also in the business of making repairs to spinning wheels.
In Conclusion
It seems that creating tools for fiber artists has come to me at a good time. It’s nice to turn something small so that I don’t have to use a hoist to get it on the lathe, LOL! Unlike many woodturners, I really enjoy production work. It challenges me and keeps my skills sharp. Some of you may identify with that. Most of all, it is very satisfying when people get their own enjoyment from something that I make, whether it is to please the eye, do a job well or, better yet, do both at the same time.